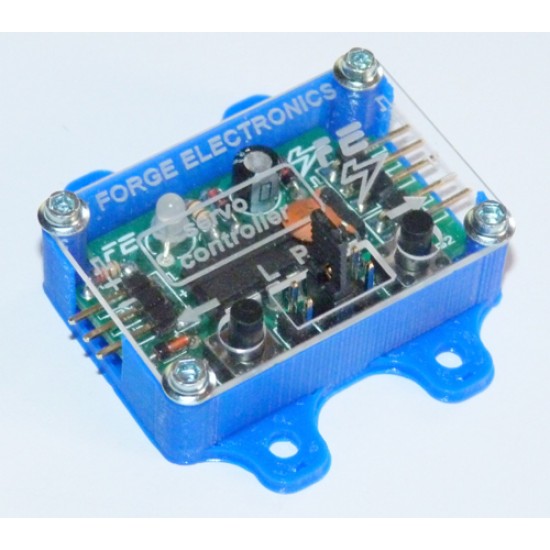
Servo Controller
An Improved Servo Controller by A F Bond Forge Electronics 2014
This unit was designed to improve the use of servos driving guns on model warships. It sits between the receiver and the servo and performs both servo slowing and stretching functions. Thus up to 180 degrees of rotation can be obtained, the gun precesses slowly and smoothly when the joystick is held left or right and holds its position when the joystick is released. At the limits of rotation a logic output goes low which can be used to trigger gunfire from a suitably attached sound effects module.
Many modellers choose to use a standard servo as the motive platform for a ship's guns, but driving the servo directly from a spare channel of the receiver has three main drawbacks. Firstly it is very difficult to move the gun slowly and smoothly especially if trying to operate other functions of the model at the same time and unrealistically rapid and/or jerky motion usually ensues. Secondly to maintain any position other than dead ahead, the transmitter joystick must be held at the equivalent position for the duration that the gun displacement is required. Finally, the standard signal from an RC receiver can only move a servo through 90 degrees, whereas 180 degrees is ideally required to allow a gun to fire broadsides. Gearing up the servo shaft is an option, but only serves to increase the jerkiness and maybe introduces backlash too.
Thus some time ago now, I developed a servo controller module to fit between the receiver and the servo to overcome the above problems. Firstly I arranged for joystick movement either side of a centre dead-zone to commence movement of the servo in the appropriate direction at a steady speed regardless of the size of the joystick displacement. Releasing the joystick to the central position caused the servo to halt and maintain the position achieved. The speed of travel was user adjustable from the slew rate of the servo (maybe a second or two from end to end) to around 30 seconds for a full traverse.
Secondly, by increasing the range of the servo drive signal it was possible, depending on the actual servo used, to achieve up to 180 degrees of movement. Often, the servo mechanics are asymmetric and dictate that this range is achieved as eg 70 degrees one way and 110 degrees the other, so in this example the servo horn would need to be fitted displaced by 20 degrees from its normal position to achieve the +/- 90 degrees required by the gun.
The original controller had a complex set-up procedure that could only be invoked at switch-on and used a single potentiometer to sequentially set up the anti-clockwise limit of rotation, then the clockwise limit and finally the speed of rotation. Thus, modifying any one of those three parameters meant the other two had to be re-set.
THE IMPROVED SERVO CONTROLLER
A larger version of the previously used micro-controller chip provides more code space and i/o (input/output) capability which has allowed me to program a simpler set-up procedure, accessible at anytime, not just switch-on, without the interaction between settings described above. A further (active low) output has been added which is asserted when the servo reaches either its clockwise or anticlockwise limit - this is for the purpose of automatically initiating gunfire or some other appropriate sound from a "Sparkfun MP3 Trigger" sound module. This is a low current logic output direct from the chip and may not be suitable to operate sound units other than the above. An LED also shows the status of the unit, being lit if the servo is at either of its end limits and flickering whilst the servo is in transit.
The final issue addressed is servo behaviour at power up. The original servo controller output a 1.5mSec nominal mid position signal which (for no servo movement at switch on) assumed symmetric end limits had been set and the servo had been parked at centre position at power down. The new unit allows the user to choose the position the servo assumes at power-up. Correctly chosen to suit the user application, at switch on this can avoid large displacements of the servo at maximum slewing rate which is undesirable - certainly aesthetically and maybe mechanically too if the servo is moving a large gun for example.
The kit includes the fully tested pcboard with box, instructions and a mask template for milling the slots etc for the LEDs and servo lead connectors.
£25.00
Ex Tax: £25.00
- Stock: 5
- Model: FE02 Servo Controller
- SKU: FE02 Servo Controller